1ボールペンの芯を構成する要素は、大まかに言って4つあります。インク、インクを入れる細長いインクタンク、先端のボール、そしてボールを保持しインクタンクからインクを供給するチップです。
インクタンクは、まあただのパイプ材ですのでともかくとして、性能を決めるポイントはインク、ボールとチップと言う事になります。
インクについてはいずれ改めて書こうと思いますので今回は割愛して、この稿ではボールと、特にチップについて説明します。
先ずボールペンの先端に使われるボールは、素材としては、ステンレス鋼、タングステン、セラミックス、プラスチックなどが使われています。
インクやチップを自社生産する大手メーカーでも、ボールは他社から購入しているようです。
筆記具以外の他の工業製品でもベアリングなどで球体はよく使われるので、専門の業者が多いようですね。
次回では、それぞれのボールの特徴と製造方法を解説します。
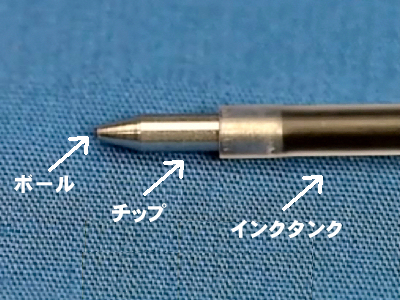
2ステンレスは、鉄に錆びにくくするためのクロムやニッケルを含ませた合金鋼で、100円クラスの安価なボールペンによく使われる素材です。
ステインは錆び、ステイン-レスで「錆び無し」という意味ですね。
材料の段階では長〜い丸棒(線材)で、ブツブツと小さく切断したのち球体に圧縮成型します。
ウィキペディアには「安価に製造できるが、若干耐磨耗性に劣る。」と書いてありましたが、実際に使えばインクが無くなるより早くボールが駄目になることは無いですよね。
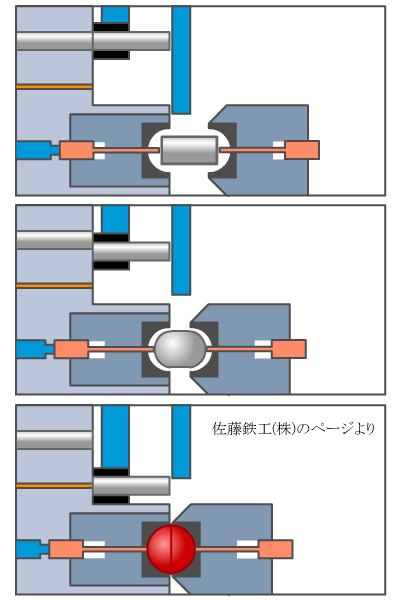
タングステンは元素記号もついている自然界にある金属で、原子番号74、元素記号は W。銀灰色の非常に硬く重い金属です。
そのタングステンに炭素加えて熱するとタングステンカーバイト(又は炭化タングステン)と呼ばれる粉末になります。
この炭化タングステンの粉末にコバルトを僅かに加えて、丸い型に入れて圧縮し、さらに熱を加えて焼結したものがタングステンボールです。
このプロセスで成型したタングステンは超硬合金と呼ばれ、非常に硬く寿命が長いので、様々な工業製品に使われているようです。
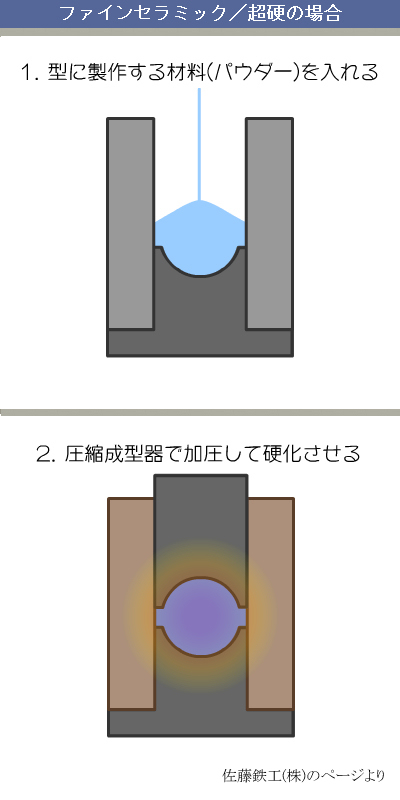
3セラミックスとは一般には陶磁器のことですが、工業的には基本成分が金属酸化物で、高温での熱処理によって焼き固めた焼結体を指します。
私にもよく分からないのですが、土や粘土を焼いて作るお皿ではなく、粉末の金属を型で焼き固めたもの、と言うことらしいです。
ボールペンのボールに使われるのは主に酸化アルミニウム(アルミナ)の粉末で、これを丸い型に入れて焼き固めてボールにします。
アルミはタングステンと同じ天然の元素で、原子番号13、元素記号はAl。
ただしアルミの形では採掘されず、鉱石であるボーキサイトを採掘し、そこから色々化学反応を引き起こしてアルミナを取り出し、さらにそこからアルミを取り出すんだとか。(汗)
磨耗が少ないため寿命が長い他、インクに対して化学変化を起こさず、表面に微細な凹凸がありインクのノリが良いそうです。
タングステンもアルミナセラミックも粉末状の状態で型に入れ、焼き固めます。このような熱をかけて固める熱硬化性とは逆に、冷まして固まる熱可塑性素材の代表がプラスチックです。
プラスチックは主に石油から作られ、細かい粒の状態で成型器に入れられ、一旦熱して溶かした状態で丸い型に流し込み、冷やして固めます。
プラボールは、ボールぺんてるなど一部の特殊なボールペンで使われていますが、柔らかく、ちょっとサインペンっぽい書き味になります。
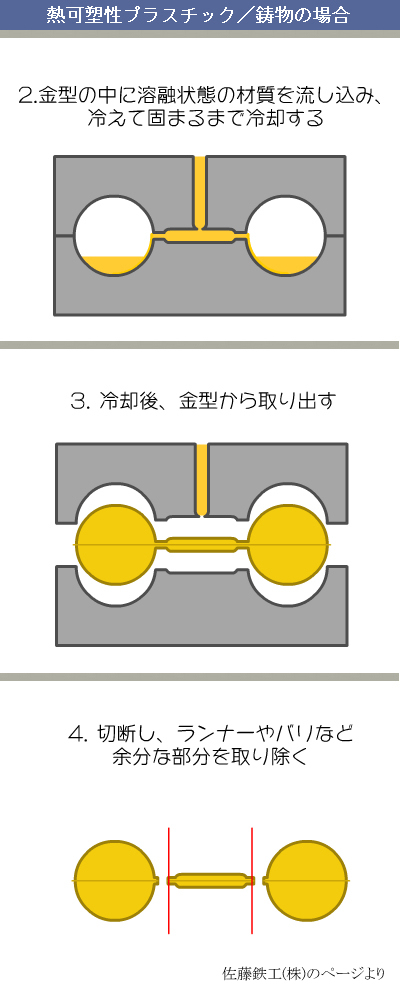
4ここまではボールの素材毎の成型方法を説明してきましたが、それらはあくまで最初の段階での大まかな成形です。
成型時には、ゲート口と言われる材料の入り口の跡や、パーティションラインと言われる型の合わせ目の跡などがありますので、ここからバリ取りなどの行程を経て、真円にしていかなければなりません。
先ずはボール素材を溝のついた2枚の円盤で挟み、圧力をかけてグリグリと転動させ、球状を整えていきます。
この行程を何段階かやりながら、バレル研磨や焼き入れ、洗浄処理、防腐処理やメッキ等の処理を行っていきます。
バレルはドラム式洗濯機のような槽に玉と研磨剤と水を入れ、ガラガラ回す方式の研磨行程で、金属加工品のバリ取り等に使われる方法です。
焼き入れは、日本刀を鍛える時などにも使われる方法で、熱した鉄を水にジュッと入れて急冷し、硬く引き締めます。
これらの方法を何段階にもわたり、最初は荒く、だんだん細かい目の研磨剤を使って表面をツルツルにしていきます。
玉の素材によって、当然、行う行程と行わない行程がありますが、ともかく真円が出ていないとボールがスムーズに回りませんので、非常に良く研磨された玉が使われているようです。
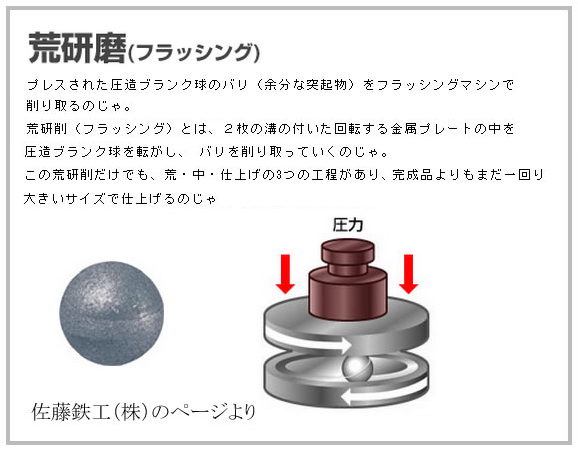
5先週までは、ボールペンのボールについての解説をしてきましたので、今週からはいよいよ本題であるチップに説明に入って行きます。
チップはボールペンの先端にあり、貫通穴の空いている小さな棒で、片側でボールを保持し、反対側でインクタンクに繋がり、インクをボールに誘導します。
ボールが先端にカシメられて、ボールと一体となった状態の部品の事をチップと呼ぶこともあります。
チップの素材は、以前は真鍮、今は快削ステンレス鋼で、パイプからではなく、棒材から切削して製作します。
棒材からの切削というと、以前にこのうんちくコラムでも連載した旋盤による挽き物加工が思い浮かびますが、このチップについては汎用の旋盤ではなく、かなり特殊な専用機で、切削だけでなくボールのカシメまで一気に行います。
実はこの連載を開始するに当たり、ボールペン製作企業の老舗であるオート株式会社の結城工場に見学に行って来ました。
その特殊な専用機の紹介をしながらチップの製作工程を開設していきます。

オートの結城工場チップ棟
6オートの工場にあるチップ製造の専用機は、スイスのアルベ社製の工作機械で、はっきり言って全世界のチップ製造機のほとんど全てがこの会社の物です。(現在、社名は変わっているそうです。)
つまりオート製であろうと、ゼブラ製であろうと、チップの品質はある程度一定に上がっているとも言えます。
かなり複雑な複合加工機で、10工程以上の加工を一つの機械の中で同時進行で進めていきます。
チップの材料のステンレス鋼は、最初は長いワイヤー状の棒の状態で工場に入荷し、細く短い棒に切断され、機械の中へ送り込まれます。
そして端からチップの材料を入れると、もう片方の端から、ボールのカシメまで終わったチップが完成されて出てきます。
こう書くと、材料が機械の内部をベルトコンベアで運ばれていく光景をイメージする方が多いと思います。
この機械の特徴は、ベルトコンベアの相当部分が円盤状になっていて、円盤が少しずつ回転することによって材料を運んでいく点にあります。
その円盤の円周上に小さな加工機が並んでいて、ちょうどリボルバーの拳銃のように、一加工が終わる毎に、材料は次の行程へと運ばれます。
そのため機械の外観は、太い筒を立てたような形をしています。
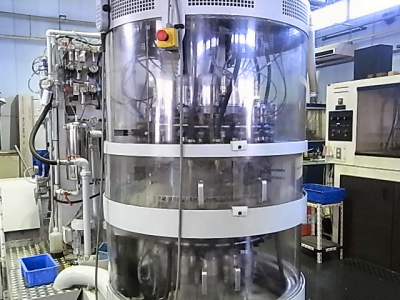
7一枚の円盤に複数の加工行程を配置しているため、全ての加工は同じタイミングで行われます。
一つの加工が終わると、円盤が僅かに回転し、円周上に置かれた材料が次の行程の行われる位置まで移動します。
円盤が回って材料が移動する際には、円盤状に置かれた全ての材料が同時に動くことになります。だから円周上で行われる各行程は同じタイミングで終了しなければならないのです。
このところは文章だと分かりにくいので、是非サイトのイラストで確認して下さい。
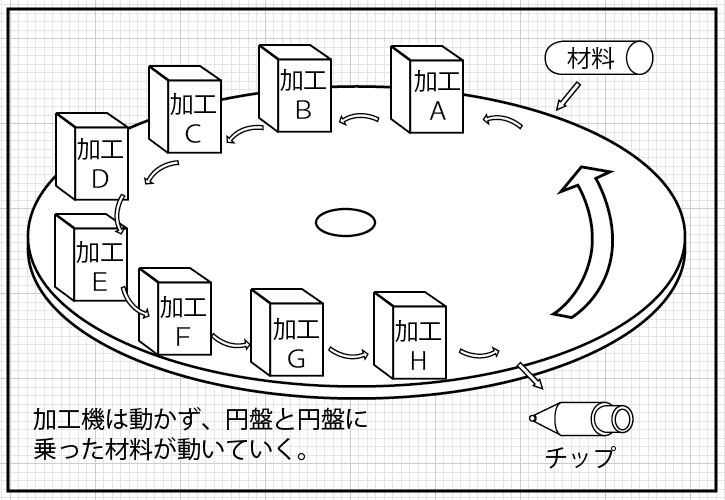
行程としては、次のような加工が順次行われます。
インクタンクに刺さるための外径削り、
ペン先の斜め削り、
後ろから大きな穴を空ける、
前からボールの入る凹みを掘る、
ボールがインクへ向かう溝穴を掘る、
ボールを後ろから押すためのバネの入る凹みを掘る、
バネを入れる、
ボールを入れる、
ボールをカシめる、
ここのところは、あまり正確な記述になっていないかもしれません。
大体このような加工が一つの機械の中で順次行われていると思って下さい。
8先週まででアルベの機械が行うチップ製作の工程を列記しましたので、今回はその各行程をもう少し細かく見ていきます。
先ずステンレス鋼の棒材の外側を削って、後ろ側にはインクタンクに刺さるように段をつけ、前側はボールに向かう傾斜を削ります。
そしてインクの通る穴を、後ろ側から先端近くまで空けます。(この時点では貫通させません。)
ボールが収まる先端部分には、ボールがガタつき無くピッタリ収まるようにボールほぼと同サイズの半球形の穴を、前側から掘ります。
ただしボールとボール受けの凹みがあまりにピッタリだと、インクが前方へ上手く流れて行きません。
流れたとしても、流れやすい箇所にインクの流れが集中してしまい、インクの出がムラになるのです。
そこで、半球状に掘られた凹みの十字方向にさらに4つの溝を掘り、その溝をインクが伝わるようにします。
それにより4方向から均一にインクが流れてムラ無くスムーズな筆記が可能になります。
このところも文章だと分かりにくいので、是非サイトのイラストで確認して下さいね。
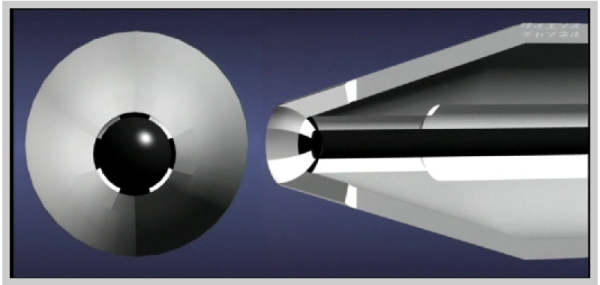
9先端にボールの入る凹みができると、その凹みにボールが入れられ、カシめて固定されます。
カシめるとは一言で単純に言うと、金属の一部に力を加えて変形させて二つ以上のものを固定することです。
例えばホッチキスでは、針を曲げて紙と針を固定していますが、あれも一種のカシメですね。
このボールペンチップの場合では、ボールを入れた凹みの縁を内側に少し倒し込み、ボールが転がり出てこないようにすることになります。
アルベのチップ製造機では、ここまでの行程を一つの機械の中で一気に加工しています。
ボールまで取り付けられ機械から出てきたチップは、専用の洗浄機に入れられ洗浄と脱脂をされます。
チップの切削作業では大量の金属の切りかす(切り粉)と熱が出ます。
そのため加工中には機械は密閉され、熱冷ましと切り粉を流れ落とすために大量の油をビチャビチャに浴びせながら加行を進めます。
切り粉や切削油がチップに残っていると、インクが詰まったり変色したりしますから、洗浄と脱脂は徹底的に行われます。
10又最近では、筆記時の力でボールがボール受けの凹みに押しつけられボールの滑らかな回転を阻害されないよう、ボールを後ろから押す為のバネがチップ内に入れられています。(全ての種類ではないようですが)
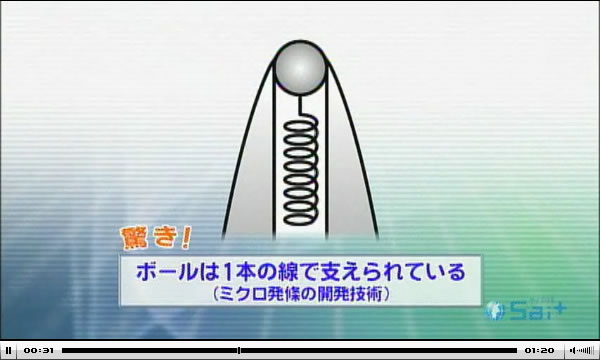
このバネは非常に小さいながらも精巧なバネで、例えば細字の0.5mmボールペンの場合で、0.14mmのステンレスの針金製で、外径0.97mmのバネになるそうです。
しかも金属のボール球を支えるためにバネの先端には人差し指を立てたように1本の針金を突出させ、0.14mmの針金が球と1点で接する構造となっていて、その先端部はボールが回転しやすいように半球形に加工
されています。
さすがのアルベ製の機械でもこの微細なバネを組み込むことはできないため、脱脂後に別の専用機でチップの後ろからバネを入れ、蓋をしてバネが出てこないように加工します。
この専用の微細なバネを製作できるのは世界でも数社しかなく、中でもトップシェアを誇るのが長野県諏訪市にある(株)ミクロ発條で、なんと国内シェア70%、世界シェア50%だそうです。
以下のページでは、ボールペン用のバネを製作している様子が動画で
見られます。とっても興味深いので是非ご覧ください。
http://saiplus.jp/special/2008/07/02.php
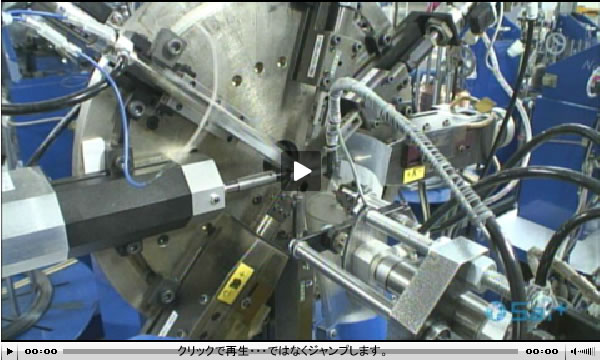
チップが完成すると、いよいよインクタンクに圧入され、インクが充填されて中芯が完成します。
インクの充填のタイミングは、中芯の種類によってチップ圧入前に行うタイプと、圧入後に行うタイプに分かれます。
一般的な安いポリ芯や、インクタンクが細い場合は、タンクにインクを注入してからチップを圧入します。
チップを先に圧入してしまうと、空気が先端から出なくなってしまい、インクが後ろから入って行かなくなるからです。
粘度の高い油性インクの場合、先端が塞がれていないタンクにインクを注入しても、タンクの細さと粘度の高さでインクは前からこぼれません。
それに対して主に粘度の低い水性インクや、インクタンクが太いタイプの場合は先にチップを圧入し、その後に長い注射針を後ろからタンクに刺してインクを注入します。
タイプによってはタンクの後ろに蓋がされ、中芯の完成となります。
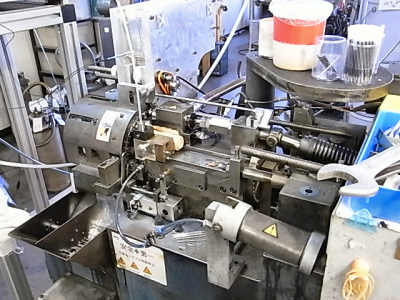
(おしまい |