開発編
開発秘話などと大げさなタイトルを付けはしましたが、実際のところ、このベークライトのボールペンについては、あまり秘話めいた長い話はありません。
下請けからの脱却を量ろうと夢見てキリタのオリジナルボールペンの品揃えを模索していた頃、数少ないラインナップに上げられていた候補の製品は、どれも真鍮製の、その頃桐平工業がメインで生産していたOEM製品の焼き直し品ばかりでした。
どうも同じような製品ばかりで面白くないと悩んでいた所、現場の技術責任者である加川課長が提案してくれたものが、このベークライトボールペンでした。
「品揃えが不足しているのならこんな物はどうだろうか。これなら材料も、かなり昔に買って残った物が相当あるし。ただし、これは1本1本削るから一度にたくさんは作れないけどな。」
そう言って見せてくれたのは、少し黒ずんだ焦げ茶のボディーで、先端金具が無く1本の棒から削り出したことの分かる、触った感触の柔らかい樹脂のボールペンでした。
そのベークライトの素材は、かなり以前に当時の社長の気まぐれで、釣りのリールのハンドル製作用に買ったもので、余分に買いはしたもののリピートが無く置き去りにされていた棒材でした。
「この材料は元はもっと明るい茶色なんだけど、使っていくと黒ずんだ良い艶になっていくんだ。材料が余っているんで、俺は勝手にボールペンに仕立てて自分用に使っていたんだけど。」とのこと。
この人いつの間にこんな物を作っていたんだ、とも思いましたが、確かに物を見ればなかなか風合いがあって良さげなボールペン。
真鍮の固いボールペンばかりのラインナップに、1本位はこんな変わったボールペンが有っても良いんじゃないかと思えてきました。
ただ、価格設定についてはかなり悩みました。
キリタの一番の技術者である加川課長が自ら時間を取って1本ずつ削り、量産も効かないとなれば、相当の価格にしなければ合いません。
結局、1本当たりどの位の製作時間がかかるのかを調べつつ、他の手作り万年筆屋さんの価格なども参考にして、2万5千円の価格を設定しました。
いざ販売を始めて見ると、開業当時のキリタの中では最も高い製品であるにもかかわらず、ぽつりぽつりと注文も入り、量産出来ないペンとしてはちょうど良い感じで販売が続いていきました。
その後、キャップ式の水性ボールペンもベークのラインナップに加え、かなり評判良く現在まで続いています。
ここからは、ベークの素材についてと、切削方法などを解説します。
素材編
ベークライトは最も古くから使われている樹脂の一種でフェノール樹脂とも呼ばれています。
樹脂(プラスチック)には、熱をかけるとドロドロに溶け、型に流し込んでから冷やして固める「熱可塑性樹脂」と、熱をかけることによって硬化する熱硬化性樹脂があります。
ベークライト(略号PF)は熱硬化性樹脂の代表的なもので、一般的なプラスチックとは異なり熱をかけても溶けない性質を活かして、様々な製品に使われています。
発明されたのは1872年(明治5年)ですが、1909年(明治42年)になってドイツのベークランド博士によって工業化されました。
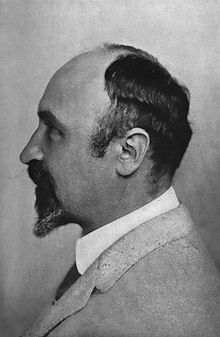
彼の名を付けたゼネラルベークライト社のフェノール樹脂の商品名であるベークライトが、今では素材名であるかのように一般的に使われています。
実際にはあくまで商品名なので、日本でも住友ベークライト以外の会社から出ているものには、ベークライトの文字がありません。
熱硬化性で熱に強いベークライトのもう一つの特徴は絶縁性です。この熱に強く電気を通さない特性を活かして、昔から最もよく使われたのが電球のソケットやヤカンの取っ手などです。
今では電球自体があまり使われなくなってきていますが、昔はベークライトと言えばソケットのイメージがありました。
最近よく使われているのは、やはりその特性を活かしてプリント配線基板ですね。あの、電気製品の中にある、緑の回路が乗っかっている板です。絶縁で熱に強い性質が回路の基板としてピッタリなのですね。
日本でベークライトの供給メーカーといえば、大阪の利昌工業がトップメーカーです。キリタでもベークライトボールペンの素材は利昌さんから購入しています。
その利昌工業のサイトを見ても、現在の商材の中心は回路用のプリント基板で、キリタでペン用に使っている棒材は、サイト内でもなかなか見つける事は出来ません。
利昌工業さんのHPはこちら。
http://www.risho.co.jp/
熱硬化性樹脂であるベークの棒材の作り方は、「熱可塑性樹脂」のプラスチックの棒材とはかなり異なる作り方になります。
実は私もよく知らないのですが、ベークの棒材には紙ベークと布ベークがあり、ベーク樹脂を浸した紙または布を巻き上げて棒状にするそうです。
そのために断面がロールケーキのような年輪のような感じになり、その棒材を削り出していくことによって木目に似た風合いが出てきます。
ベークライトの色は、黒か茶が一般的なようです。そういえば電球のソケットは今は白ですが、昔は大抵は黒でしたね。
ただ今では、プリント基板がメイン商材になったため茶色がメインで、黒色のベークはほとんど生産されていないようです。
この茶色のベーク棒のもう一つの特徴は、使っていくうちに徐々に艶のある黒ずんだ色に変色していくこと。
棒材としておいておくだけでは変色はしてこないので、たぶん手の脂に反応するのでしょうか。(この辺は勉強不足で、しかとは分かりません。)
何年かかかって徐々に出てくる黒の艶が、とても良い味を醸し出します。
使い続けるのが楽しみなペンです。
このベークは、削る際に独特の匂いが出るのですが、これがまた慣れるといい匂いだったりします。
パソコンに向かって仕事をしていても、あの独特の匂いがしてくると、あぁ今日はベークを削る日なんだなと、すぐに分かります。
万年筆などの筆記具に使われて来た樹脂素材と言えば、セルロイドやエボナイトが一般的ですが、ベークライトも戦前から使われて来ました。
これらの材料を使う場合は、現代の型に流し込んで冷やして形を取るプラスチックとは異なり、既に固まった棒状の材料から1本1本削り出していくことになります。
全て職人による手作業で、それ故に量産はできずかなり高価な製品となります。現在では、日本でも数人しか職人は残っていません。
轆轤(ろくろ)と旋盤
棒材を削って万年筆などの筆記具を作る場合には、戦前から日本の職人たちの間では、ろくろ(轆轤)という特殊な旋盤が使用されてきました。
そもそも一般に人には旋盤による切削にイメージがないかと思いますが、こけしや野球のバットなどを削るように、機械に取り付けた棒材を高速回転させて刃物を当て、削っていく方法だと思ってください。
リンゴの皮むきも、刃物を当てて回転させるという点では同じですね。
現在一般的な旋盤では、材料の棒材は、自分から見て横になるように旋盤機に取り付けられます。
それに対して轆轤では、先端が自分に向いている、刀を突きつけられるような向きで棒材を機械に取り付けます。
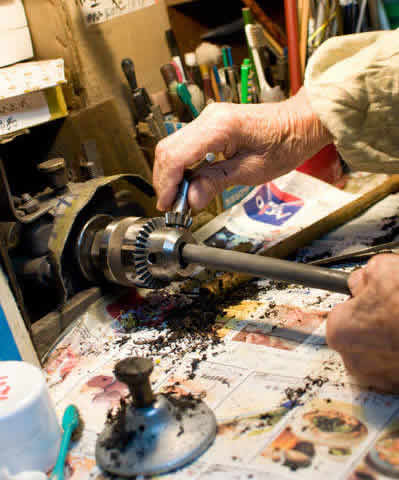
一般の旋盤では刃物も機械に固定しますが、轆轤によるペンの切削においては、刃物を手に持ったまま回転する材料に押し当てて削ることが多いので、手の角度からして、棒が自分を向いている方が刃物を当てやすいのです。
そして昔の足踏みミシンのように、足下のペダルを踏むことによって、棒材を回転させます。電気を使わずに、自分の体力だけで切削作業をしていたのですね。
現在の電動で動く通常の旋盤では相当のスピードで材料を回転させています。
しかし轆轤でのペン作りでは、手で直接刃物を当てることを考えると、その時々のタイミングで微妙に速度を遅く調節できる方が削りやすく、安全でもあるのです。
足踏みによる自力での回転だからこそ、その辺の微妙なスピードコントロールが可能なのですね。(現在では、電動との両用のようです。)
ここで面白いのは、ペダルには右足用と左足用があり、踏み分けることによって右回転、左回転が自在に、そして瞬時に切り替わるようになっていることです。
ドリルは回転方向を変えなくても引き戻すことができますが、ネジ切りタップは逆回転をさせなければ引き戻すことができません。
これはドリルでの穴あけや、ねじ切りなどの作業を行う際に、回転を瞬時に逆に切り替えることによって、ドリルやねじ切りタップを切りすぎずに引き戻すのに便利な仕掛けなのです。
このように、轆轤職人は轆轤を体の一部のように自在に操って、万年筆などを作り出していたのですね。
と、ここまで書いてくると、ベークライトボールペンも轆轤を使って削りだしているのかと思うかもしれませんが、実はキリタでは轆轤を使っていません。使っているのはペンチレースと言われる卓上旋盤です。
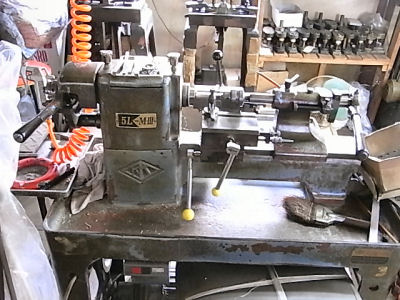
柔らかい樹脂なら自走の轆轤でもまぁ削れますが、キリタが扱う材料は主に真鍮。元々が手作り万年筆の会社ではなく、旋盤による金属加工の会社ですから轆轤の設備はありません。
逆に言えば、便利な轆轤を使わずに電動の卓上旋盤のみで削り出しの筆記具を作っていく方がより困難で手間がかかり、職人の高い技術を必要とすることになります。
大まかに切削の手順を言うと、先ず外観より先に中心の穴を空けます。
外観を削ってから穴を空けようとすると、棒材が細くなっている分だけ回転が安定しません。
ドリルでの穴明けには相当の力が加わるので、棒材の太さのまましっかりと安定して回転していないと、穴のセンターずれや、最悪折れなどにも繋がります。
いきなり大きな穴を空けようとすると抵抗が大きいので、大抵は先に細い下穴を空けてから何回かに分けて穴を大きく空けていきます。
穴は先端に行くにしたがって小さくなり、特にボールペンの場合では先端は芯の通る細い穴を空けることになります。
穴はだんだん小さくなっていきますが、ペンの外側のようになだらかなカーブを描いて小さくなる訳ではありません。
ドリルでは先端部分でしか穴を空けられないので、穴の内径はドリルの外径のまま真っ直ぐにしか空かないからです。(図にすると簡単ですが、言葉にすると分かりにくいですね。)
そのため先端に行くにしたがって穴を細くするには、ドリルを何度も交換して、太いドリルでは浅く掘り、そこから先は細いドリルで深く掘ることによって、段々で細くなる穴にします。
あるいは、部位によっては途中に段の付いた半月ドリルを使います。
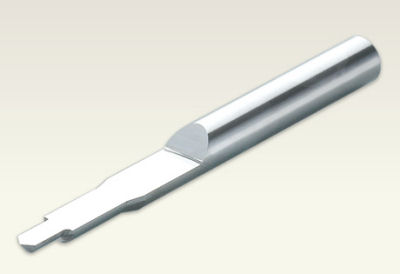
半月ドリルについては、以前に金属挽き物についての連載をしていた際に解説しましたのでバックナンバーを参照して下さい。
http://www.kirita-pen.jp/magazine/BN/2011/110715.htm
穴を空けた後に外径の削りを行います。この行程で難しいのは、やはりきれいなカーブを描いて表面を切削していくことでしょうか。
棒材に穴を空けるには、最初はどうしてもドリルを使いますが、ある程度穴が開いたら、バイトで穴を広げることもあります。
中ぐりバイトという先端がくの字に曲がったバイトを穴に入れて内側から旋盤加工で切削をします。
ペンの先端近くの穴は小さいのでくの字に曲がったバイトを入れる事ができませんが、穴が大きくなるペンの中心付近については、この方法もよく使われます。
ドリルを使うとどうしてもまっすぐな穴にしかなりませんが、中ぐりバイトを使って旋盤的に穴を広げる場合は、縦の動きと横の動きを同時に与えられるため、斜めの穴を空けることもできます。
外径を削るときも旋盤の縦の動きと横の動きを組み合わせたバイトの動きで棒材を斜めに、丸みもつけて削っていきます。
轆轤で削る場合は手に刃物を持ち、直接材料に当てて斜めや丸みもつけて行ってしまうようですが、轆轤が無く旋盤を使うキリタでは、あくまでも旋盤的に削っていきます。
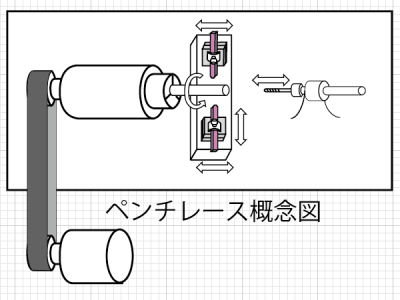
ペンチレースと呼ばれる卓上旋盤では、棒材をチャックで固定して回転させ、そこにバイトと呼ばれる刃物をおし当てて材料を削ります。
その際バイトはカンナ台と呼ばれる刃物台に固定され、そのカンナ台をレールに沿って縦方向と横方向に動かしてバイトを材料に当てていきます。
かんな台はレバーで動かします。レバーといっても「スイッチ、オン!
ガチャ、」というタイプのレバーではなくてレバーはカンナ台に直結しており、レバーを動かした分だけカンナ台が動くようになっています。
このレバーが縦方向用と横方向用にそれぞれ付いていて両手で動かします。
通常、量産品の部品の2次加工などをする場合には、縦方向と横方向を同時に動かすことはあまりなく、横を動かしてから縦あるいはその反対の順番で別々に動かすことが多いのですが、両手で同時に動かすことにより、斜めや丸みをつけた切削も可能になります。
(カンナ台を斜めに設置すれば、縦方向の動きだけでも斜めに削ることもできます。)
先にも述べたように、カンナ台は、直結したレバーを手で動かして動かします。つまり動かす人の手加減・力加減で微妙な曲線(丸み)を付けることができるので、ペンの先端や後部の丸みはこの方法で丸く削っていきます。
轆轤(ろくろ)で直接刃物を当てる技術の白眉は外径へのネジ切りです。
普通はダイスというネジ切り用の工具を使いますが、轆轤では鋸のようなギザギザのついたバイトを直接手で当ててネジを切ってしまいます。
NC旋盤なら刃物の動きと材料の回転を制御して一般的に行われている方法ですが、それを手でやるのは実に見事な物です。
実は私も随分以前にテレビで見ただけなのですが、回転している材料に櫛歯をちょっと当てて離すだけで、もうネジが切れていました。
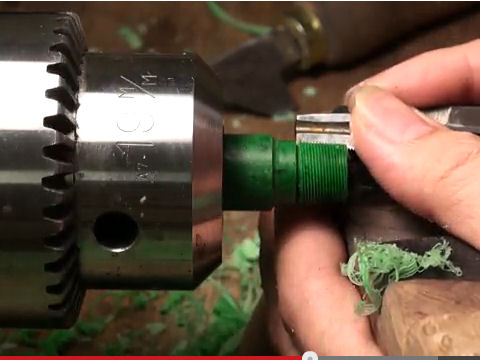
轆轤のないキリタではダイスを使ってネジを切っていますが、ダイスを材料に噛ませて、それを回転させてネジを切り、逆回転させてダイスを抜くのは、櫛歯を当てるのに比べてかなり面倒な作業になります。
職人の加川に、轆轤があれば楽なんでしょうねと言ったら、もう長年これでやっているから苦にならないよと言っていました。(笑)
穴を空け、表面の形を作り込み、ネジを切ったら、後は表面をヤスリで整えて、バフで磨くと、ベークの本体部分が完成します。
轆轤の由来
このベークライトとその棒材を加工する挽き物(ろくろ)についての解説を始めて、すでにかなりの回数を数えましたが、ベークライトの製造元である利昌工業さんから先日メールをいただきました。
利昌工業は大阪の会社ですが、広報室の吉岡さんは、私の連載に興味を持っていただき、なんと滋賀にあるろくろについての縁起の地域を訪ねて、写真を送っていただきました。m(_ _)m
いただいたメールによると、滋賀県東近江市君ケ畑にある大皇器地祖神社と蛭谷にある筒井神社が「木地師発祥の地」であるとのこと。
「木地師」というのが今のろくろ職人のことで、木材を使って椀・盆などを作っていた人達のようです。
滋賀県の観光情報によると、ろくろ挽きは、平安時代、文徳天皇の第1皇子であった惟喬(これたか)親王が巻物のひもにヒントを得て考えついたといわれていて、その技術を蛭谷・君ケ畑の人々に伝授した縁起により、親王がろくろ業の祖神として両神社に祀られているそうです。
筒井神社境内には木地師資料館があり、ろくろを使った全国の伝統ある木地製品をはじめ、木地師の伝統や文化を今に伝えている氏子狩帳や往来手形などの古文書類の数々が展示されています。
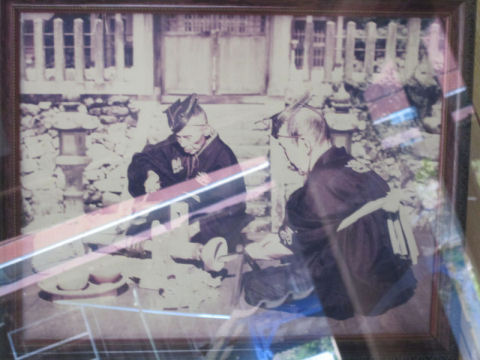
利昌工業の吉岡さんによると、滋賀県君ケ畑にある「金龍寺」には、なんと「ろくろと万年筆」という石碑があるそうです。
いただいたメールによると、「建立に関わった会社として、モリソン万年筆、パール万年筆製作所、スケーター万年筆、センター万年筆、日出万年筆といった社名のほか「東京万年筆事業協同組合」(日本筆記具工業会の前身)の名前もありました。」とのこと。
う〜ん、正直な感想としては、かなり微妙〜です。
なぜなら、上記の会社は全て今は無い会社か、有っても万年筆の製造
から手を引いて問屋になっている会社ばかりなのです。
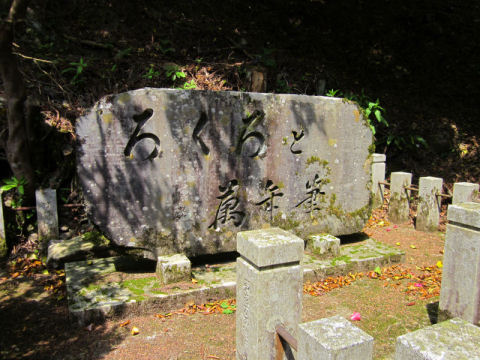
今も存在している日本の万年筆メーカーはパイロット、プラチナ、セーラーの3社だけです。(ペン先を自社で作り、一定の規模がある会社)
ろくろによる1本ずつの製造を止めて、プラスチック成型による大量生産に切替えた会社のみが残った訳です。栄枯盛衰、諸行無常ですね。(もちろん成型が悪い訳でもないし、3社の技術は素晴らしいです。)
ただそれでも、ろくろによる1本削りの万年筆が全く作られなくなってしまった訳ではありません。
職人さんがほとんど個人で営んでいるろくろ工房が、全国に何カ所か残っています。
昔ながらの万年筆工房
今も旋盤挽き物(ろくろ)を使って万年筆を製作をしている個人工房としては、以下のようなところでしょうか。
大橋堂(宮城)
中屋万年筆(東京)
川窪万年筆店(東京)
masahiro万年筆製作所(静岡)
万年筆博士(鳥取)
大西製作所(大阪)
笑暮屋(東京)
Stylo Art (長野)
惜しいことに、ここ数年の間に大橋堂の植原氏、加藤製作所の加藤氏、ロングプロダクツの藤本氏などが他界されていて、減ってきているのが現状です。(大橋堂はどなたかが後継されているようです。)
本体素材についてはエボナイトを使う所、セルロイドを使う所、そして銘木を使う所に分かれます。
ペン先については(昔からの特別なつてで)国内メーカーから仕入れている所と、海外のパーツメーカーから購入している所があるようです。
いずれにしても、自社でペン先を作っている所は無いですね。手作り万年筆を謳っていても、あくまで本体軸の手作りということです。(ペン先の調製は、している所が多いようです。)
これらの手作り万年筆工房のほとんどは、1人の職人が製作している個人工房ですが、中屋万年筆だけはプラチナ万年筆の子会社で、組織もしっかりした会社になっています。
プラチナの職人の再就職先にもなっているようで、プラチナのパーツを使い、価格も高く、蒔絵なども扱っている超高級工房です。
仙台の大橋堂さんと鳥取の万年筆博士さんは手作り万年筆の大御所でしたが、大橋堂の植原栄一さんは2010年に他界、博士の田中晴美さんは2011年に勇退されました。現在は、跡を継いだ方が工房を引き継いでいるようです。東京の川窪万年筆さんも、おそらく2代目さんですね。
静岡市のmasahiro万年筆製作所の内野さんは、そのサイトを見る限り、相当こだわりの強い職人さんのようです。年齢的にも今が脂の乗りきった職人さんのようです。
社歴が比較的新しいのは大阪の大西製作所さん、東京荒川の笑暮屋さん、軽井沢のStylo Artさんです。
大西さんは、大阪のカトウセイサクショの加藤さん、ロングプロダクトの藤本さんの流れをくむ旋盤加工屋さんで、加藤さんらの設備や材料を継承しているようです。
大阪という街は何故か文具のネットショップが集中している街で、多くの文具系ネットショップが盛んに大西さんの万年筆を販売しています。
笑暮屋さんはその母体が、現在も日本でエボナイトを作っている唯一の会社である日興エボナイトです。
本来はエボナイトを供給する会社なのですが、エボナイトの需要の減少もあり、数年前から自らエボナイト製品の製造販売を始めました。
日興エボナイトで万年筆の製作をしている金崎さんは、万年筆好きが高じて職人になったまだ若い職人さんですが、東京のおじいさん職人を訪問して教えを受け、ろくろも譲り受けたという研究熱心な青年です。
私は日興の遠藤社長と金崎さんの双方と面識がありますが、この2人の出会いを(勝手に)奇跡の出会いと思っています。(今度機会があったらそのいきさつを聞いておきますね。)
自然豊かな軽井沢にある数野元志氏のStyloArtでは、本体に銘木を使った万年筆をメインに製作しています。
桑、山桜、黒檀、紫檀、花梨などなど、様々な銘木を使った万年筆はとても購買意欲をそそる物ばかりで、私もいつか手に入れたいと思っています。
銘木を使った万年筆はとても魅力的なのですが、他の工房ではあまり銘木は使われていません。
それは工業的に作られたエボナイトやセルロイドに比べると、木はいざ削り始めたらうろがあったり場所によって堅さが異なったりと個体差が大きく削りにくいからでしょう。
また、万年筆メインではないので先のリストには載せませんでしたが、岐阜にある工房「楔」でも銘木を使ったペンを製作しており、こちらもとても良い風合いの作品になっています。
店名 |
所在地 |
本体素材 |
ペン先仕入れ先(想像) |
大橋堂 |
宮城県
仙台市 |
エボナイト |
セーラー? |
中屋万年筆 |
東京都
文京区 |
エボナイト |
プラチナ |
川窪万年筆 |
東京都
文京区 |
銘木、エボナイト、 |
パイロット? |
masahiro
万年筆製作所 |
静岡県
静岡市 |
エボナイト |
パイロット |
万年筆博士 |
鳥取県
鳥取市 |
セルロイド/エボナイト/銘木 |
セーラー/パイロット |
大西製作所 |
大阪府
生野区 |
セルロイド |
シュミット? |
笑暮屋 |
東京都
荒川区 |
エボナイト |
Bock(独) |
Stylo Art |
長野県
軽井沢 |
銘木 |
? |
工房 楔 |
岐阜県
羽島市
|
銘木 |
シュミット |
キリタのベークライト万年筆
こ数回の連載で、棒材から削り出す手作り万年筆の話をしてきました。
元々は、ベークライト素材を使ったキリタの手作りボールペンの話をするつもりだったのですが、だんだん話がそれてしまいました。
今もある手作り工房として代表的な9社を紹介しましたが、そこで使われている材料は主にエボナイト、セルロイドと銘木でした。
ベークライトを使っているのは、ほぼキリタだけです。
今まではボールペンと水性ボールペンしか製作していませんでしたが、棒材から手作りで削り出して製作している筆記具という点では上記の9社と同じ事をしているわけです。
という事は、万年筆のペン先(首軸)だけ調達できれば、ベークライト製の手作り万年筆がキリタでも作れると言う事です。
実際、以前にも述べましたが、上記の万年筆工房でもペン先は製造しておらず、いずれも外部調達です。
今まで万年筆というとマニア色が強く、ちょっと敷居が高く感じていましたが、ここで新しいチャレンジとして、キリタでも万年筆を製作してみようと言う事になりました。
2005年のネットショップオープン時から、ペン工房キリタでは一貫して万年筆の製造販売をしてきませんでした。
その理由は、キリタのメイン製品が真鍮製の重いペンであり、ペン先を潰さないように浮かせ気味に使う万年筆では重いペンは向かないことがありました。
また、万年筆は扱いが面倒で愛好者が使う筆記具であり、ギフトに適した万人向けのものではないこと。
さらに、ペン先は仕入れになるため、ペン先の太さやインクの品揃え、ぺン先の調製などの点で、十分なサービスができないことも、発売に踏み切れない理由でした。
しかしベークライトという軽めの素材で、1本ずつの少量生産するのであれば、このような「やらない理由」もかなりの部分は回避できます。
ペン先については、ドイツのシュミット製ステンレスを使っています。シュミットはドイツにある世界最大の筆記パーツメーカーで、日本でもパイロット、プラチナ、セーラーの3大メーカー以外の多くの筆記具メーカーがそのペン先を採用しています。
キリタでは、シュミットの日本総代理店である大阪のプリコ商事とお付き合いがあり、その関係もありシュミット製のペン先を採用しました。
そしてもう一つ、今回の発売に至った本当の理由は、ベークライトのボールペンを製作している職人の加川が、自ら望んで万年筆を作ってみたいと言ってきたことです。
ベークライトのボールペンでは数年前からキャップ式の水性も製作していて、ペン先以外の部分が作れることは分かっていました。
加川としても、ここまでできるのであれば、筆記具の王様である万年筆も世に出したいとの思いが募ったのでしょう。
加川は職人歴40年。この製品はいわば彼の作品であり、敬意を込めてこの製品の名前を「加川」とします。
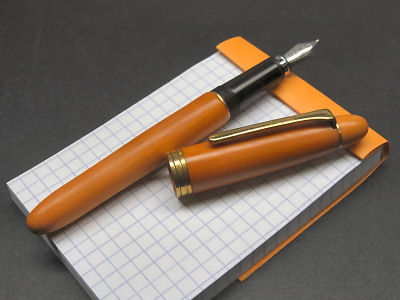

万年筆の製品ページはこちらから
利昌工業さんについて解説したページはこちら
http://www.kirita-pen.jp/linnku/trivia/risho.htm
|