ここではプレスによる鉄製クリップの製造過程を解説していきます。
言葉による説明が難しい工程ですが、なるべく分かり易く書いていきますね。
まず全工程を極く簡単に一言で言うと、平たく薄い鉄の板を展開図の形で打ち抜いて、曲げて曲げて曲げて形を作っていき、焼き入れで硬くして仕上がりとなります。
そもそもプレスとは、対象物を挟み込んで押しつぶすという意味で、アイロンもプレスですし、サッカーの戦術でも使われる言葉ですね。
工業においては、出っ張った雄型と引っ込んだ雌型の間に薄い金属板を置き、型と型を思いっきり叩きつけるように組み合わせることで、金属板に対して「抜き」「絞り」「曲げ」などの加工を行います。
「抜き」とは、金属板を型の形に打ち抜くことで、書類を綴じるためのパンチ穴を想像していただければ良いかと思います。
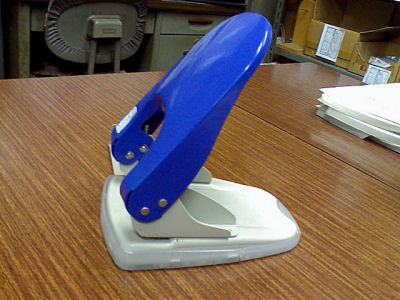
穴を開けた時に出る丸いカスが、プレスで打ち抜かれた形になります。
最近では動物やトランプなどの形に穴が空くお洒落なパンチも売っていて、この場合は打ち抜かれた方をノートに貼ったりして使うようです。
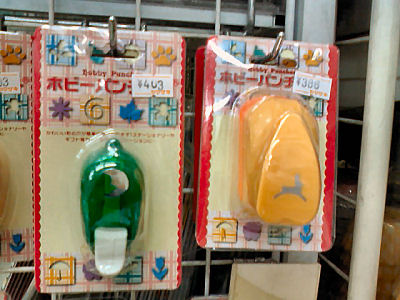
ペンクリップの場合、ペーパークラフトの立体工作のように、最初は展開図の形で板から打ち抜きます。
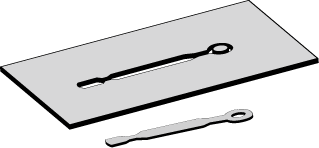
展開図の形で板から打ち抜いたクリップは、「絞り」工程で形を盛り上げます。
金属板を雄型と雌型で、瞬間的に強い力でガッシャンと挟み込むことによって、金属が薄く伸びて、型の形に変形します。
例えば金属製のお釜などはこの方法で形を出します。
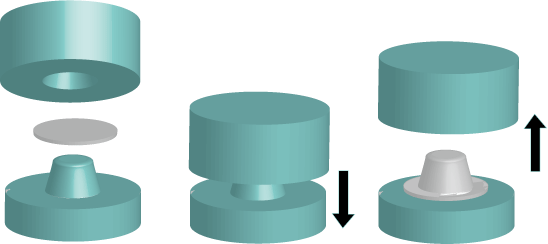
ただの板状のまま展開図の形に打ち抜かれていたクリップは、この「絞り」によって立体的に膨らんだ形になります。
当然、金属が伸びた分は、その部分の板の厚さは逆に最初より薄くなります。
そしてクリップの縁や、先端のボール状に丸くなった所などは、次の「曲げ」工程で、再びガッチャンとプレスされ、折り曲げられて形が作られていきます。
全ての部分を一度に曲げることはできないので、曲げる部位毎に型を変えて何度もプレスすることになります。
クリップが90度に曲げられてペンに取り付けられる部分では、一度のプレスでは曲げきれずに、2・3回に分けて少しずつ曲げていきます。
こうして見ていくと、一つのペンクリップを作るには何度も型を変えて何度もプレスを掛ていく必要があるのが分かります。
型もその工程毎に必要なので、クリップ一つに7・8個の型を製作しなければならず、そのための費用も100万円を軽く越えることも珍しくありません。
プレスを行うための装置には大きく分けて「単発」「順送」「トランスファー」の3種類があります。
どの装置を使うかによって、型もそれ対応の型になり、同じ型を別の装置で使用することはできません。
ちなみに材料の薄い金属板は、帯状に横にず〜〜〜っと延びてクルクル巻かれた状態でプレス屋さんに届きます。それを少しずつ繰り出して使っていくんですね。
昔からある「単発」装置は、1つの型だけを取り付けられる比較的小型のプレス機です。
形が単純なものや、工程数(プレスを行う回数)が少ないクリップの生産には今も使われています。
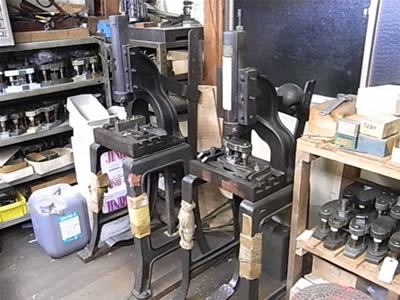
(この写真はキリタ内にあるケトバシと呼ばれる簡易プレス機です。)
クリップの生産数分のプレスが打ち終わると、打ち終わったクリップは回収されて、型の交換をして次の工程のプレスを行います。
それを繰り返して全ての工程を行うのですが、型の交換にも手間取りますし、クリップを一つ一つ置いていく作業がたいへんなこともあって、最近では大量品には使われなくなっています。
現在クリップ製作に主流で使われているプレス機(と言うか型)は「順送」と呼ばれている方式のものになります。
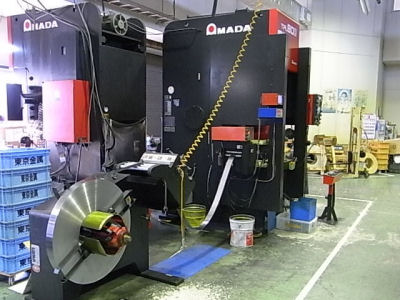
これは単発用の型をまとめて一列に並べているかのように、1つの型の中に全ての工程の雄型と雌型を彫り込んでしまう方法です。
一度のガッチャンで全ての工程がプレスされるのですが、ちょっとややこしいので以下の説明をよく読んでくださいね。
まず、帯状に伸びている材料の端を、型の最初の工程部分にかかるようにセットして、1回目のガッチャンをします。
仮に5工程分の形状が彫り込まれている型であれば、残りの4工程に相当する場所では、材料が無い空打ちになります。
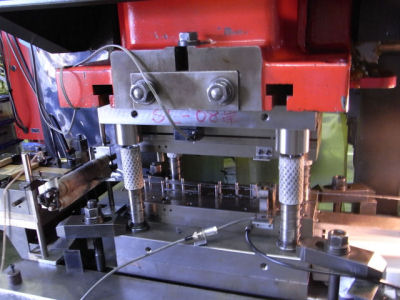
最初の工程は当然展開図での打ち抜きになりますが、この時に完全に打ち抜いてしまうとクリップが帯からぽろっと落っこちてしまいます。
クリップが帯から落ちてしまうと、それを集めて回収しないと次の工程に回せません。
そこでクリップ自体を完全に打ち抜かずに、クリップの周囲を抜きクリップの端っこは帯に繋がったまま残します。
1回目のガッチャンが終わると、材料の帯を1工程分だけ奥に送り込みます。
型の第1工程相当場所には新しい材料板が入り、第2工程相当場所には、周囲を打ち抜かれて1カ所で帯と繋がっているクリップの展開図が入ります。
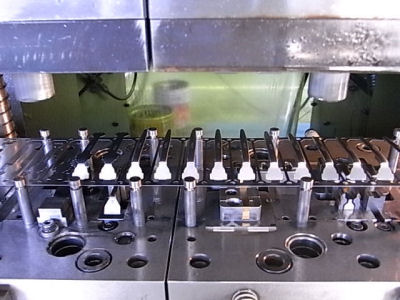
その状態で2回目のガッチャンを行うと、第1工程部分では打ち抜きが行われ、同時に第2工程部分では絞りが行われます。
残りの3工程部分では空打ちになります。
さらに材料の帯を1工程分だけ型の奥に送り込みガッチャンすると、第1工程部では打ち抜きが、第2工程部では絞りが、第3工程部では曲げが行われ、残りの2つの箇所が空打ちになります。
そうして順に材料帯を送って行き、第4工程の曲げでクリップの形が整うと、最終第5工程では帯からクリップが切り落とされます。
繋がった帯が型を縦断し、1回のガッチャン毎にそれぞれの部署でそれぞれのプレス加工が同時に行われることになります。
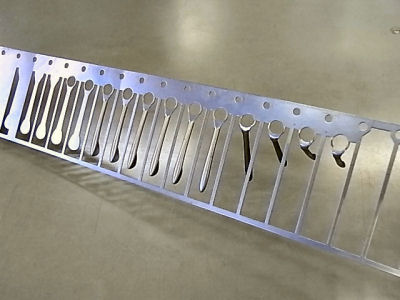
それを連続で行い、長い帯を少しずつ送り出して使っていきます。
抜きが終わって機械から出てきた抜け殻の帯は反対側で再び巻き取られていきます。
材料の帯を順送りで送り出し、1つの型の中を順送りで形が整っていくので「順送式」と呼ばれているんですね。
人手がかからずに大量生産ができることが特徴の順送式ですが、欠点としては、全ての工程が彫り込まれている型なので、どこか1つの工程で型の不良が起こっても、丸々全ての工程を含む型ごと修理や保守をしなければならないことでした。
最悪型ごと作り直しをしなければならない場合には、悪くない部分も
捨てることで相当無駄が出ます。
それらの問題を解決するために、クリップのトップメーカーである東京金属工業が開発したのがコアブロック交換タイプの順送型です。
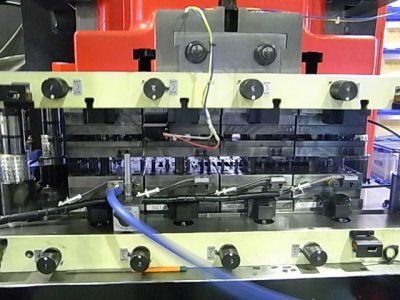
この型では、1つの順送型の中で、それぞれの工程部分が取り外せるようになっており、型の交換修理や部分変更、バリエーション作りなどが、格段にやりやすくなりました。
型の費用も大幅に削減され、これからの型の主流となるそうです。
最後にトランスファー型とは、大きな装置に単発の型を横に並べたようなものです。それぞれの型は連動してはいても別々の型でになります。
大がかりな装置で、ペンの本体プレスなどにはよく使われても、ペンクリップにはあまり多くは使われていないようです。
プレスの工程が終了し、クリップの形が出来上がると、次に焼き入れをして鉄を硬くします。
焼き入れとは、金属を高熱の炉に入れて熱〜くした後に、水の中にジュッと入れて急激に冷ます行為で、これをすると不思議に鉄がコチコチに硬くなります。
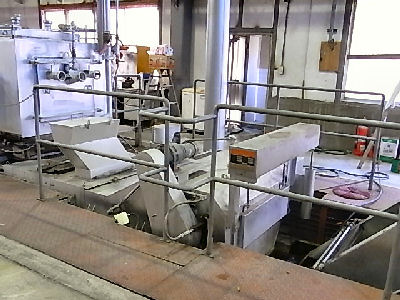
製鉄所から届けられる材料の鉄は、プレスで曲げる必要があるため、柔らかい仕上がりのものになっています。
このままの状態だと、プレスを打ち終わったクリップにも曲がって元に戻るバネ性はなく、指でもくにゃっと潰れてしまいます。
プレス後のクリップは、ベルトコンベアの装置の付いた大きな焼き入れ装置に入れられると、炉を通って冷却水槽に入り、さらに錆止め液の水槽を通って出てくると完成になります。
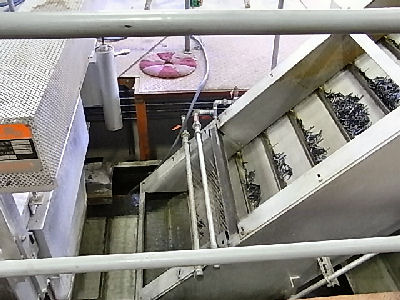
単に硬くなるだけでなく、バネ性のあるしなりが出るのが不思議ですね。
この焼き入れにも、炉の温度や時間、冷やすタイミング等にノウハウがあって、材質や大きさによって色々な装置(と言うより設備)があるようです。
ペンクリップの種類
ペンクリップの東京金属工業
|